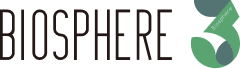


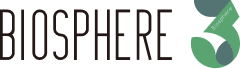



The Forge will be the first Net Zero Carbon development Landsec are developing. It comprises two buildings, one c.90,000 sq ft and the other c.40,000 sq ft, with a beautiful public realm courtyard.
Zero Carbon London
→ BREEAM ‘Excellent’ rating
→ 44% reduction in CO2 against Part L, surpassing the GLA target
→ 22% reduction in embodied carbon
→ 100% renewable electricity
→ WELL v2 enabled
The Forge will be the first Net Zero Carbon development Landsec are developing. It comprises two buildings, one c.90,000 sq ft and the other c.40,000 sq ft, with a beautiful public realm courtyard.
Landsec was the first commercial real estate company in the world to have its carbon reductions target approved by the Science Based Targets Initiative in 2016. As part of this commitment, The Forge, Landsec’s new build office development in Southwark, is aiming to be the UK’s first net zero carbon commercial building. This means the building will be both constructed and operated in line with the UK’s Green Building Council (UKGBC) framework definition of net zero carbon buildings.
It is a pioneering project and the first major commercial building to be built using a platform approach to design for manufacture and assembly (P-DfMA). The project has been awarded funding from Innovate UK for its innovative design and ground-breaking construction techniques, which has the potential to act as a catalyst for change in the construction sector. This approach has resulted in a 19.4 per cent reduction in embodied carbon emissions against a typical build baseline which is being driven down further through the design development.
In order to minimise operational energy use in line with UKGBC targets, Bryden Wood have used passive design techniques before adopting the use of highly efficient electric air source heat pump (ASHP) systems to provide heating and cooling from a 100 per cent renewable electricity tariff. Photovoltaic panels (PVs) are provided at roof level to offset the annual emergency generator diesel fuel consumption resulting from ongoing maintenance operation.
Embodied carbon was tackled through lean design and the P-DfMA approach led to a componentised solution that is integrated and optimised. Offsite manufacturing significantly reduces material waste and material specifications ensure high levels of recycled content and cement replacement in main building materials. Overall, the project is achieving a 22 per cent reduction in embodied carbon compared with the baseline.
Design for Performance was used to model the operational energy of the building in much more granularity than required for compliance. An all-electric solution run on renewable tariffs was selected, minimising impact on global emissions as well as on local air quality.
Forge将是Landec正在开发的第一个净零碳开发项目。它由两座建筑组成,一栋约90,000平方英尺,另一座约40,000平方英尺,并设有一个美丽的公共庭院。
零碳伦敦
→ BREEAM“优秀”评级
与L部分相比,CO2减排量→44%,超过GLA目标
→ 隐含碳
减少 22%→启用 WELL v2 → 100% 可再生电力
Forge将是Landec正在开发的第一个净零碳开发项目。它由两座建筑组成,一栋约90,000平方英尺,另一座约40,000平方英尺,并设有一个美丽的公共庭院。
Landsec是世界上第一家在2016年科学碳目标倡议组织批准其碳减排目标的商业房地产公司。作为这一承诺的一部分,Landsec在南华克新建的办公楼开发项目The Forge的目标是成为英国第一座净零碳商业建筑。这意味着该建筑的建造和运营将符合英国绿色建筑委员会(UKGBC)对净零碳建筑的框架定义。
这是一个开创性项目,也是第一座使用平台方法进行制造和组装设计(P-DfMA)建造的大型商业建筑。该项目因其创新设计和突破性建筑技术而获得了Innovate UK的资助,这有可能成为建筑行业变革的催化剂。这种方法使隐含碳排放量比典型的建筑基线减少了19.4%,而典型建筑基线正在通过设计开发进一步降低。
为了根据UKGBC目标最大限度地减少运营能源使用,Bryden Wood在使用高效电空气源热泵(ASHP)系统之前使用了被动设计技术,以100%可再生电价提供供暖和制冷。光伏板(PV)在屋顶提供,以抵消因持续维护操作而导致的年度应急发电机柴油消耗。
隐含碳通过精益设计得到解决,P-DfMA方法导致了集成和优化的组件化解决方案。异地制造大大减少了材料浪费,材料规格确保了主要建筑材料的高回收含量和水泥替代。总体而言,与基线相比,该项目的隐含碳减少了22%。
性能设计用于对建筑物的运行能量进行建模,其粒度远高于合规性要求。选择了采用可再生能源电价的全电动解决方案,最大限度地减少了对全球排放和当地空气质量的影响。



0
收藏


提交评论
相关内容